Revolutionizing Prosthetics: The Power of Digital Design at Limber
- Samantha Obligacion
- Mar 27
- 3 min read
Digital design has revolutionized the prosthetics industry by making the process of creating prosthetic devices more efficient, precise, and personalized. With the advent of advanced technologies such as 3D scanning, CAD (computer-aided design) software, and 3D printing, prosthetic manufacturers can now design and produce highly customized prostheses through entirely digital processes that result in improved precision, faster production, and improved performance. This blog discusses the advantages of digital design in the prosthetics industry and describes how Limber remains at the forefront of this innovative revolution.
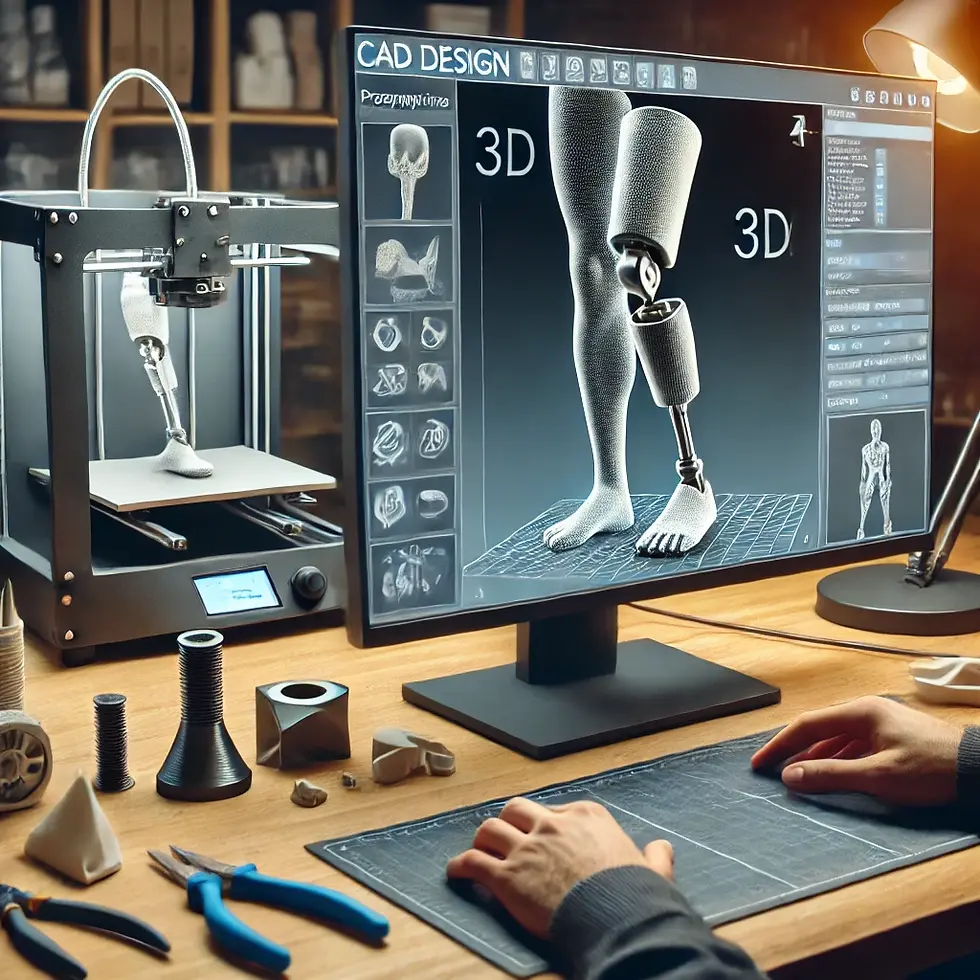
One key way digital design has impacted the prosthetic device industry is through its ability to increase precision and customization of devices. Digital design allows for precise measurements of an amputee's residual limb through 3D scanning. Integrated with solutions like COMB Scan and Structure, Limber’s proprietary mobile phone app captures precise imaging of residual limbs of patients. This data is used to create a virtual model of the limb, which enables designers to craft a prosthetic socket with an exact fit. The custom fit enhances comfort, reduces pressure points, and minimizes skin irritation, all of which improve the overall user experience.

Secondly, digital design presents the advantage of faster production. By using digital design tools like CAD software, prosthetic designs can be quickly modified and optimized for each individual case. This eliminates the need for multiple fittings or manual adjustments. Digital design combined with 3D printing facilitates an efficient manufacturing process compared to manual traditional methods. A digital workflow allows prosthetists to move from design to production in a fraction of the time, reducing turnaround times for patients. Furthermore, automating aspects of the design process with digital tools reduces material waste and can lower labor costs. 3D printing technology, in particular, allows manufacturers to produce prosthetics with complex geometries and lightweight materials at a lower cost. This makes high-quality prosthetics more accessible to a broader population, especially in low-resource settings.
Improved performance and durability of the prosthesis can be added to the list of advantages of digital design. Digital design software enables manufacturers to test the structural integrity and performance of prosthetic components in a virtual environment. This reduces the risk of errors and allows for fine-tuning of the prosthetic’s strength, weight distribution, and flexibility before physical production. This leads to more durable and functional devices that can better withstand daily wear and tear.
Lastly, the most widely impactful advantage of digital design in the prosthetics industry is its ability to expand access to safe, durable, cost-effective prosthetic devices in all regions and also creates the possibility of remote collaboration amongst prosthetists and manufacturers across the globe. Digital tools enable remote collaboration between prosthetists, engineers, and medical professionals. A prosthetist can scan a patient’s limb and share the digital file with manufacturers in different parts of the world. This global access is particularly beneficial for underserved regions, where local manufacturing capabilities may be limited.
It is evident that digital design is transforming the prosthetics industry and Limber remains at the forefront of this revolution by harnessing the most innovative modern technology. By integrating advanced technologies into clinical workflows, Limber offers fully customized, precise, and durable prosthetic solutions like the UniLeg for below-knee amputees. The Limber UniLeg is the world’s first fully 3D printed transtibial prosthesis that is crafted through the use of scanning, digital design, and 3D printing. This innovation not only enhances comfort and functionality for patients, but also reduces production time, making high-quality prosthetics more accessible and potentially improving operational efficiency for clinics as well. Limber’s commitment to affordability, personalization, and performance positions itself as a leader in modern prosthetic technology, expanding access to life-changing devices for amputees worldwide. Together, we are shaping the future of prosthetic care. To learn more about the UniLeg, visit our website.